The Journey of Steel: From Iron Ore to Everyday Applications
Written on
Chapter 1: The Significance of Steel
Imagine a world devoid of steel—it's hard to envision, isn't it? Steel's omnipresence in our lives is so ingrained that we often overlook its importance. From the tiniest screws to the tallest skyscrapers, steel plays a pivotal role in modern construction and manufacturing. Each year, approximately 2 billion tonnes of steel are produced globally. To put this into perspective, let's delve into the process of creating just 1 kilogram of steel.
Section 1.1: Extracting Iron Ore
Iron is the fourth most abundant element in the Earth's crust, comprising about 5% of it. Consequently, iron needs to be mined from beneath the surface. Open-pit mining is the preferred method for extracting iron ore due to its cost-effectiveness and efficiency for large-scale operations. However, when iron deposits are located deep underground, underground mining is necessary.
Australia stands as the leading exporter of iron ore, followed by Brazil and China. The extensive mining operations in these countries are no coincidence; the sheer volume of iron required for steel production necessitates vast amounts of ore. This high demand underscores why extensive space is essential for mining installations.
Section 1.2: The Melting Process
The process of forging steel begins at temperatures reaching 1650°C. Remarkably, steel boasts a recycling rate of 75%, making it one of the most recycled materials available.
To obtain metallic iron from iron ore, the oxidized iron must be reduced. Not all iron ores are created equal; those with higher iron content are more desirable, as they require less energy and processing. After extraction, iron ore goes through several processing stages, including:
- Crushing: This step reduces the ore to a fine powder, aiding in iron extraction.
- Concentration: Techniques like magnetic separation or flotation are employed to separate iron ore from impurities based on their physical or chemical properties.
- Roasting: This process involves heating the ore in oxygen to eliminate impurities as gas or slag.
The conversion of iron to steel involves adjusting its chemical makeup, particularly the carbon content, to produce various steel types suitable for specific applications. This transformation takes place in steel mills, where iron is mixed with elements such as carbon, nickel, and chromium, based on the desired characteristics of the final product.
Subsection 1.2.1: Steel Characteristics
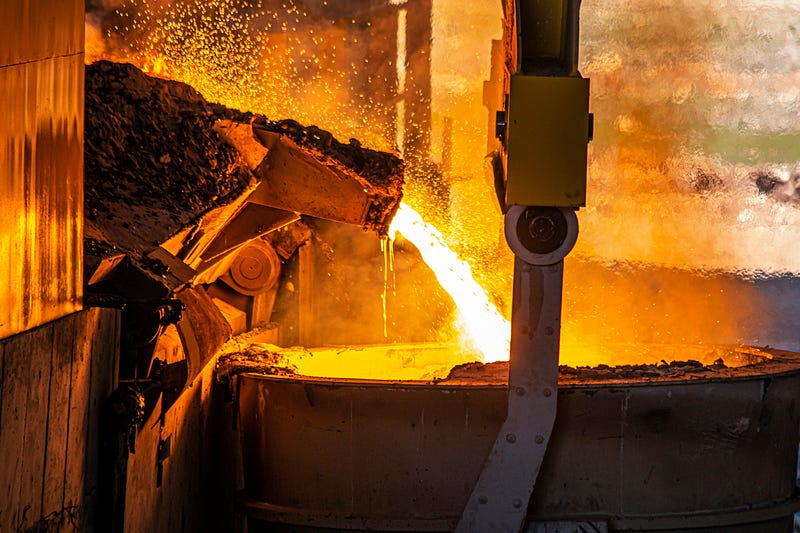
Once cooled and solidified, the resulting product is steel, which exhibits varying properties depending on the composition and concentration of added elements.
Chapter 2: Shaping Steel for Use
Steel is renowned for its strength, being approximately seven times stronger than aluminum. It maintains its structural integrity across a wide temperature range, from -40°C to 100°C, making it ideal for various applications.
After the initial casting, steel takes on various shapes, including billets, blooms, and tubes. These forms undergo further processing in rolling and forming facilities, where they are heated and molded into final or semi-finished products, such as plates, sheets, beams, and pipes.
Steel mills and service centers customize these semi-finished products based on client specifications. For instance, a steel sheet may be cut to size for an appliance manufacturer, or a beam may be tailored for a construction project. The material's versatility, durability, strength, abundance, and recyclability make it indispensable in modern society.
Final Thoughts on Steel Production
Iron Ore Extraction: Predominantly mined using open-pit methods for surface deposits and underground for deeper sources, with major exports from Australia, Brazil, and China.
Refining Process: Iron ore undergoes reduction to eliminate impurities through stages like crushing, magnetic separation, and roasting, preparing it for smelting.
Steel Production: Refined iron is alloyed with elements like carbon in high-temperature furnaces to yield steel with specific characteristics.
Manufacturing and Uses: Steel is cast into various forms, then processed to create products utilized in construction and manufacturing, owing to its strength and versatility.
As we look to the future, one wonders if we will discover materials that surpass steel's capabilities. Thank you for engaging with this exploration of steel production. Until next time!
The links provided are not affiliated. For related topics, consider exploring:
- The Unseen Environmental Impact: The Journey of Gold Production
- Discover the intricate production processes behind everyday items.